Category
- Products
- FAQ
- Contact us
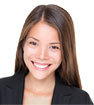
Frequency inverter manufacturers
Home » Application
Heat pump loop systems may be converted to variable flow by installing a solenoid valve on each heat pump to stop the flow of water through the local heat pump (HP), when the unit is not operating. This allows the pump head to increase and the frequency inverter to modulate the pump speed to maintain a constant head (reduced flow). The result is a demand reduction and energy savings.
In such a system, with various frequency inverters operating different pump sequences, installation costs can be reduced by installing frequency inverters with network capability. For example, frequency inverters with Metasys N2 communication bus, can be daisy chained instead of hardwired back to the controller(s).
In such a system, with various frequency inverters operating different pump sequences, installation costs can be reduced by installing frequency inverters with network capability. For example, frequency inverters with Metasys N2 communication bus, can be daisy chained instead of hardwired back to the controller(s).
Control Considerations
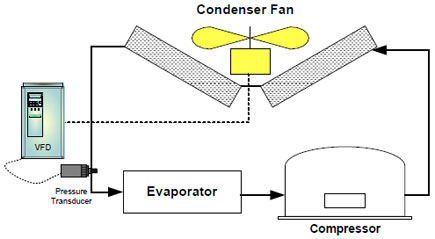
- Pressure sensor is connected to the refrigeration system and wired directly to the frequency inverter with a built in PID controller. This reduces material and installation costs.
- Consider where the frequency inverter is to be mounted. It may need to be housed in an outside air enclosure and need to operate in low ambient environment (-40 deg F)
- The existing motor may need to be converted to 3 phase.
- If the frequency inverter is to mounted a fair distance away, consider an output filter even though the motor is inverter rated.
- For sleeve bearing motors, the frequency inverter may be programmed to operate the motor at full speed for a few seconds to provide adequate lubrication of the motor.
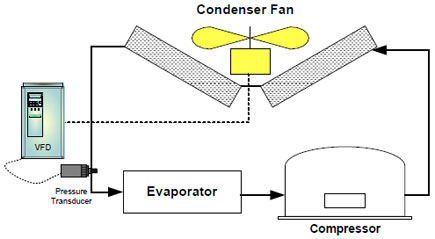
Electric motors equipped with frequency converters have been around for some time. Traditional frequency converter applications include fluid pumps, HVAC, conveyor systems, and positive-displacement rotary-lobe blowers.
Only recently have they been applied to rotary-screw air compressors. Frequency control rotary screw compressors, typically saves users 20 to 35% on electricity when applied to variable loads.
The efficiency of variable-speed compressors controlled by a frequency converter is not constant over the complete control range. Between 70 and 30% of full flow, or speed, efficiency is reduced from 94 to 86% for a 94-kW motor, for example. Added to this are losses in the frequency converter and the nonlinear performance characteristic of the compressors. If variable-speed compressors are wrongly used, they can turn into secret power eaters. This means a frequency converter is not a universal remedy in the search for maximum efficiency and power-saving compressor operation.
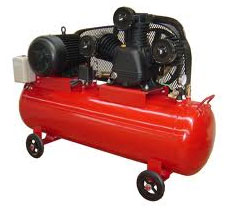
The efficiency of variable-speed compressors controlled by a frequency converter is not constant over the complete control range. Between 70 and 30% of full flow, or speed, efficiency is reduced from 94 to 86% for a 94-kW motor, for example. Added to this are losses in the frequency converter and the nonlinear performance characteristic of the compressors. If variable-speed compressors are wrongly used, they can turn into secret power eaters. This means a frequency converter is not a universal remedy in the search for maximum efficiency and power-saving compressor operation.
The booster pump and the export pump should have their own minimum-flow recycle valves. These minimum flows need to be maintained at all times -- either by a flow control valve or a restrictive orifice. A restrictive orifice is simpler; however, it will waste energy. I suggest flow control loops so that the flow is recycled only when needed. If flow above the minimum rate is required and the economics allow, use frequency inverters to reduce energy consumption.
The problems reported may be due to low seal pressure. Double mechanical seals require pressure above the pump discharge pressure. Otherwise, hydrocarbon will migrate to the seal system. Another symptom -- pump vibration at low flow -- may be due to improper alignment and cavitation. The same problems will appear with the new pump if the cause is not clearly established.
The problems reported may be due to low seal pressure. Double mechanical seals require pressure above the pump discharge pressure. Otherwise, hydrocarbon will migrate to the seal system. Another symptom -- pump vibration at low flow -- may be due to improper alignment and cavitation. The same problems will appear with the new pump if the cause is not clearly established.
Company A will save 55% of the energy costs by choosing a frequency inverter over outlet dampers and nearly 36% over inlet dampers. In addition, it may realize additional savings from the reduced equipment wear and tear that a frequency inverter provides compared to dampers.
Frequency converters reduce airflow without dampers or other mechanical controls. They allow the operator to adjust the frequency of electric power to the motor and thereby slow down or speed up the fan. frequency converters decrease flow noise and stress on equipment at reduced speeds. They often are the ideal solution, provided you can justify the initial capital expenditure.
Frequency converters may be incorporated into the original fan design or may be retrofitted to an existing fan. However, retrofits may demand important adjustments to the fan or to the coupling between the motor and fan.
Frequency converters may be incorporated into the original fan design or may be retrofitted to an existing fan. However, retrofits may demand important adjustments to the fan or to the coupling between the motor and fan.
When frequency inverters are applied to Make Up Air fan systems, potential savings are realized by frequency inverter reducing the speed of the fan during low occupancy periods. The chart below shows the relationship between power and flow. These physical laws of fans show that a 50% reduction in flow requires only 12.5% of the available horsepower. For a 50 Hp , this means that only 6.26 Hp is required.
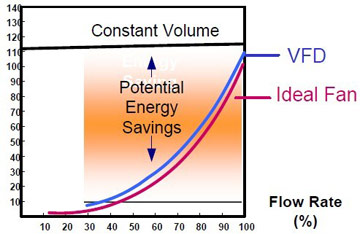
Additional energy is saved by the REDUCED amount of air that is required to be heated or cooled. Applying frequency inverters to Make Up Air systems together with a good overall control strategy can realize substantial energy savings with payback less than 2 years.
Control Application & Considerations
Scheduling the Make Up Air can be as simple has programming the frequency inverter to several preset speeds that reflect the different occupancy periods in a building. The preset speeds are activated by time clock contacts or DDC control. The DDC control provides additional benefits which include frequency inverter control, mechanical heating & cooling control with temperature setback.
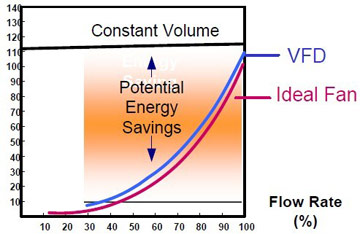
Additional energy is saved by the REDUCED amount of air that is required to be heated or cooled. Applying frequency inverters to Make Up Air systems together with a good overall control strategy can realize substantial energy savings with payback less than 2 years.
Control Application & Considerations
Scheduling the Make Up Air can be as simple has programming the frequency inverter to several preset speeds that reflect the different occupancy periods in a building. The preset speeds are activated by time clock contacts or DDC control. The DDC control provides additional benefits which include frequency inverter control, mechanical heating & cooling control with temperature setback.
Implementing frequency converter to Chiller Condenser Water Reset can be easier achieved with PLC type DDC controls, which use cooling tower supply and return temperatures to reset the condenser temperature and to monitor the load on the chiller. Additional sensors can monitor chiller load, control fan speed, and insure that the condenser water temperature doesn't drop too low.
- Use the DDC controller to control the frequency converter & calculate the reset setpoint of the condenser water.
- To ensure flow of refrigerant and maintain oil movement within the chiller, a minimum pressure differential must be maintained between the condenser and evaporator.
- Too low of condenser water will hamper return of refrigerant and actually reduce chiller efficiency.
- Implement a frequency converter control strategy that optimizes the trade off between tower fan and chiller energy consumption.
- The frequency inverter control system should be capable of monitoring real time energy consumption.
- Building Automation System (BAS) Overrides should NOT be lower than the equipments minimum speed.
- Ideally the frequency inverters being controlled should be compatible and networked with the BAS. Actual energy usage, KW and power can be read directly from the frequency inverter without the added expense of interfaces.
- Consider the frequency inverters for retrofit applications. The frequency inverters are Metasys N2 and LON ready.
Frequency inverter adjusts the speed of the fan(s) on the cooling tower by sensing temperature by way of the built in controller (PID).
The frequency inverter will run the fan at the lowest speed that will maintain the system output temperature. A temperature sensor located at the towers outlet (T1) provides the signal that varies with water temperature. The set point controller (built in the frequency inverter or external) provides proportional accurate control of the cooling tower outlet temperature further, increasing the energy savings.
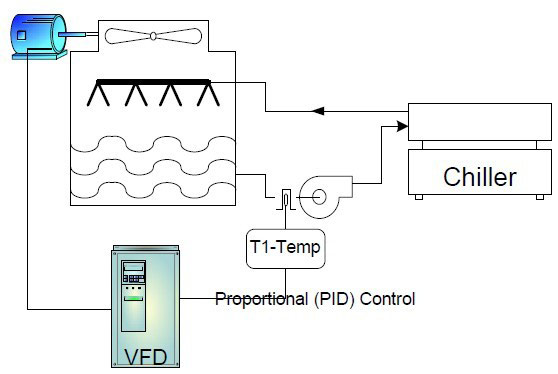
The frequency inverter will run the fan at the lowest speed that will maintain the system output temperature. A temperature sensor located at the towers outlet (T1) provides the signal that varies with water temperature. The set point controller (built in the frequency inverter or external) provides proportional accurate control of the cooling tower outlet temperature further, increasing the energy savings.
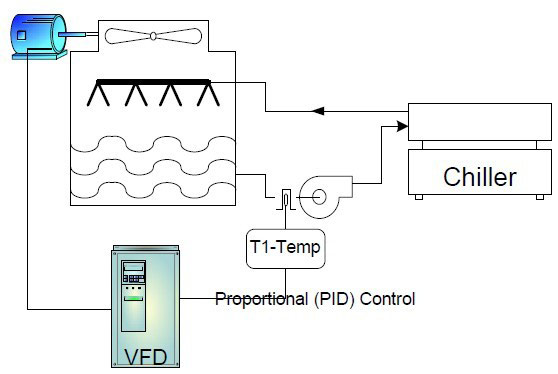
A frequency inverter is known by many names, such as variable frequency drive, frequency converter or adjustable speed drive. All mean essentially the same thing: an electronic device that provides stepless speed control in an electric motor. However, today's frequency inverters also feature other functionality, including control and protection to other equipment in the system.
Frequency converters offer the greatest savings for fans. Power is greatly reduced (more than inlet vanes) as flow and speed decreases.
Frequency converters offer the greatest savings for fans. Power is greatly reduced (more than inlet vanes) as flow and speed decreases.
It is possible to convert constant flow systems to variable flow with the use of frequency inverters. Figure 1 & 2 show two piping arrangements of constant flow systems. In these constant flow systems, bypass valves control flow but at a constant pressure and speed - which does nothing to reduce energy at part load conditions. Graph 1 shows a typical curve for bypass valve flow control.
The basic steps to convert to a variable flow system by frequency inverter are:
The basic steps to convert to a variable flow system by frequency inverter are:
- Review the systems pumping charts and system curves. If possible develop/measure your own system curves. Be sure to review or measure the systems static head.
- Review the type of valves. Three-way control valves may be converted to two way (see Figure 3). The existing 3 way valves ideally should be equal percentage, and be able to control with the added pressure they will experience. If in doubt, 2-way valves may need to be installed.
- Differential pressure sensor(s) need to be installed. The number and location of the sensor will depend on the piping system. These sensors would directly control the frequency inverters on the pumps.
- Review to determine minimum flow requirements for the equipment (boiler & chillers). A new bypass arrangement may need to be installed to maintain the minimum flow requirements.