Category
- Products
- FAQ
- Contact us
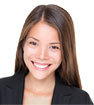
Frequency inverter manufacturers
Frequency Converter Basics
The reliability of power electronics systems is of paramount importance in industrial, commercial, aerospace, health institutions and military applications. The knowledge about the fault mode behavior of a frequency converter system is extremely important from the standpoint of improved system design, protection, and fault tolerant control. Plenty of applications can be considered critical applications meaning that they have high targets set for reliability and availability. The requirement is that no single failure would terminate the process. Appropriate means should also be used to monitor the status of the frequency converter and safety of the controlled system. There are many frequency converter system configurations that could be used, but selecting the correct system depends on the needs of the process and cost of the system.
The use of a frequency converter system in a critical application requires careful coordination of the frequency converter with the induction motor along with a method to accommodate AC power line failures. The actual needs of the process must be known to select a frequency converter system that is properly designed and provides a reasonable payback period.
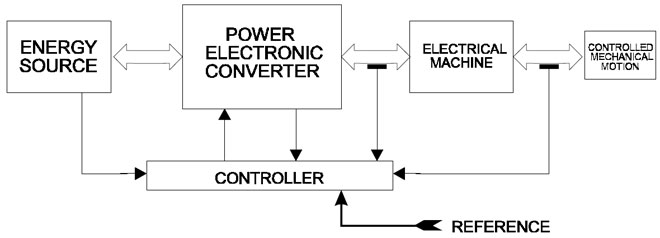
The importance of incipient fault detection is the cost saving that is realized by detecting potential failures before they occur. Currently, induction motors are required to be protected by circuit breakers of fuses that interrupt instantaneous fault currents. However these devices are intended only as safety devices and they may protect the induction motor and nearby personnel from injury due to a fault, but will not warn of potential faults before they occur. Incipient fault detection, on the other hand, allows preventative maintenance to be scheduled for machines that might not ordinarily be due for service and may also prevent an extended period of downtime caused by extensive induction motor failure. Long time disturbances in technological processes cause big economical loses.
In modern plants, thousands of induction motors work together in the manufacturing process. A portion of these applied motors are essential to the process. An unscheduled shutdown occurs if only one of these motors fails. If it was possible to detect a developing fault, for example, an interturn short circuit, then it is possible to schedule an orderly shutdown of the complete process. In these cases, it can be cost effective to continuously monitor the above-mentioned electric motors. Nevertheless, the defective motor will need to be exchanged and repaired. From this reason the problem of fast fault detection and location as well as problem of technical state evaluation (diagnostic) are very significant in the industrial practice.
A significant advance has been made in diagnostic by the introduction of artificial intelligence or expert systems. Artificial intelligence involves programming a computer so that it can mimic human thinking. An expert system essentially tends to mechanize the expertise of a human being. A human expert has knowledge, an experience base, and the power of reasoning, judgment and intuition.
Basics of frequency converters
Frequency converters are being designed into a more demanding group of applications. Originally, the applications were mostly limited to fans and pumps where the energy savings provided all immediate payback for the premium charged. Over the years, the cost of frequency converter systems has been decreasing and their performance increasing. Frequency converters are being applied to overhead cranes, continuous casters, winders, unwinders, extruders and other more demanding applications.
The AC machines, especially the cage-type induction motors, seem to process several distinct virtues in comparison with DC machines. These relate to lower cost and weight, lower inertia, higher efficiency, improved ruggedness and the capability to operate in a dirty and explosive environment due to the absence of commutators and brushes.
The speed of an induction motor is related to stator supply frequency which produces the synchronously rotating magnetic field. If frequency is increased to increase speed of the induction motor, the magnitude of air-gap flux is reduced due to increased magnetizing reactance, and correspondingly the developed torque is reduced. For this reason, an induction motor normally requires variable-voltage variable-frequency power supply for variable speed control.
There are two basic forms of power electronic converters for changing from the fixed AC power frequency to variable frequency: cyclo-converter (performs this operation in a single conversion stage) and converters with a DC-link (converter is decoupled into the two sides).
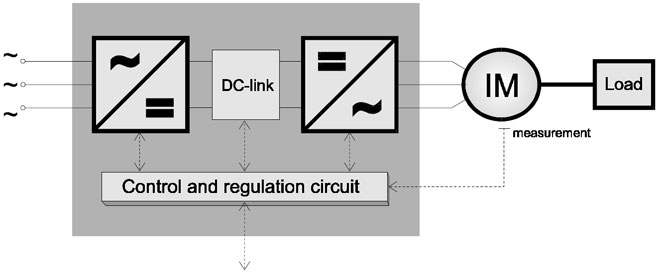
The cyclo-converter drives are used only in very large horse-power applications. The cost and complexity of power and control circuits make them uncompetitive with other classes of frequency converters in general applications.
The process of converting DC to AC power is called inversion and it is the inverter which creates the variable frequency from the DC source which is used to drive an induction motor at a variable speed. In general, two basic types of inverters exist which are totally different in their behavior. The so called Voltage Source Inverter is more common and this type of inverter creates relatively well defined switched voltage waveform at the terminals of the motor. The DC bus is maintained as voltage source by the use of a large capacitor in the DC link. A voltage source inverter differs from the voltage stiff inverter in that the DC link is established with a DC source (battery for instance). The resulting motor current is then governed primarily by the motor load and the speed. The VSI is also termed a voltage source inverter. However, it is clear that the DC link itself is truly not a power source if the link voltage is supported only by an energy storage element such as a DC capacitor. The VSI is typically subdivided into two forms the so called six step inverter and the pulse width modulated (PWM) inverter.
The second type of inverter, the Current Source Inverter (CSI) provides a switched current waveform at the motor terminals. The DC bus is maintained as current stiff by use of a large inductor in the DC link. The voltage waveform is now governed primarily by the motor load and speed.
The use of a frequency converter system in a critical application requires careful coordination of the frequency converter with the induction motor along with a method to accommodate AC power line failures. The actual needs of the process must be known to select a frequency converter system that is properly designed and provides a reasonable payback period.
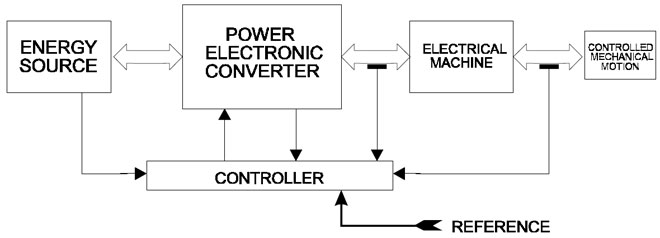
The importance of incipient fault detection is the cost saving that is realized by detecting potential failures before they occur. Currently, induction motors are required to be protected by circuit breakers of fuses that interrupt instantaneous fault currents. However these devices are intended only as safety devices and they may protect the induction motor and nearby personnel from injury due to a fault, but will not warn of potential faults before they occur. Incipient fault detection, on the other hand, allows preventative maintenance to be scheduled for machines that might not ordinarily be due for service and may also prevent an extended period of downtime caused by extensive induction motor failure. Long time disturbances in technological processes cause big economical loses.
In modern plants, thousands of induction motors work together in the manufacturing process. A portion of these applied motors are essential to the process. An unscheduled shutdown occurs if only one of these motors fails. If it was possible to detect a developing fault, for example, an interturn short circuit, then it is possible to schedule an orderly shutdown of the complete process. In these cases, it can be cost effective to continuously monitor the above-mentioned electric motors. Nevertheless, the defective motor will need to be exchanged and repaired. From this reason the problem of fast fault detection and location as well as problem of technical state evaluation (diagnostic) are very significant in the industrial practice.
A significant advance has been made in diagnostic by the introduction of artificial intelligence or expert systems. Artificial intelligence involves programming a computer so that it can mimic human thinking. An expert system essentially tends to mechanize the expertise of a human being. A human expert has knowledge, an experience base, and the power of reasoning, judgment and intuition.
Basics of frequency converters
Frequency converters are being designed into a more demanding group of applications. Originally, the applications were mostly limited to fans and pumps where the energy savings provided all immediate payback for the premium charged. Over the years, the cost of frequency converter systems has been decreasing and their performance increasing. Frequency converters are being applied to overhead cranes, continuous casters, winders, unwinders, extruders and other more demanding applications.
The AC machines, especially the cage-type induction motors, seem to process several distinct virtues in comparison with DC machines. These relate to lower cost and weight, lower inertia, higher efficiency, improved ruggedness and the capability to operate in a dirty and explosive environment due to the absence of commutators and brushes.
The speed of an induction motor is related to stator supply frequency which produces the synchronously rotating magnetic field. If frequency is increased to increase speed of the induction motor, the magnitude of air-gap flux is reduced due to increased magnetizing reactance, and correspondingly the developed torque is reduced. For this reason, an induction motor normally requires variable-voltage variable-frequency power supply for variable speed control.
There are two basic forms of power electronic converters for changing from the fixed AC power frequency to variable frequency: cyclo-converter (performs this operation in a single conversion stage) and converters with a DC-link (converter is decoupled into the two sides).
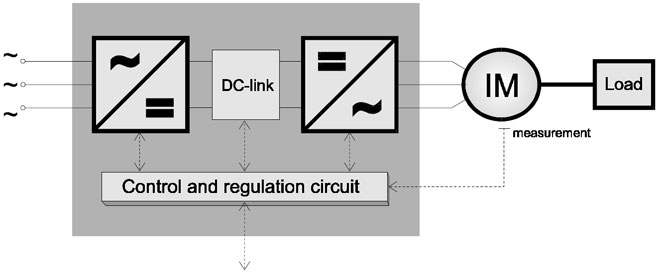
The cyclo-converter drives are used only in very large horse-power applications. The cost and complexity of power and control circuits make them uncompetitive with other classes of frequency converters in general applications.
The process of converting DC to AC power is called inversion and it is the inverter which creates the variable frequency from the DC source which is used to drive an induction motor at a variable speed. In general, two basic types of inverters exist which are totally different in their behavior. The so called Voltage Source Inverter is more common and this type of inverter creates relatively well defined switched voltage waveform at the terminals of the motor. The DC bus is maintained as voltage source by the use of a large capacitor in the DC link. A voltage source inverter differs from the voltage stiff inverter in that the DC link is established with a DC source (battery for instance). The resulting motor current is then governed primarily by the motor load and the speed. The VSI is also termed a voltage source inverter. However, it is clear that the DC link itself is truly not a power source if the link voltage is supported only by an energy storage element such as a DC capacitor. The VSI is typically subdivided into two forms the so called six step inverter and the pulse width modulated (PWM) inverter.
The second type of inverter, the Current Source Inverter (CSI) provides a switched current waveform at the motor terminals. The DC bus is maintained as current stiff by use of a large inductor in the DC link. The voltage waveform is now governed primarily by the motor load and speed.
Post a Comment:
You may also like: