Category
- Products
- FAQ
- Contact us
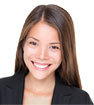
Frequency inverter manufacturers
Frequency Converter Monitoring
Most modern frequency converters operate by converting a three-phase voltage source to DC and use insulated gate bipolar transistors (IGBT's) to switch the DC voltage on and off at typically 3000 to 4000 hertz. Varying the duration or width of the individual pulses [pulse width modulation (PWM)] controls the effective voltage. To help "shape" the synthesized sine wave, intermixed positive and negative pulses are used at lower displacement of the synthesized sine wave.
Measuring the Voltage
True RMS measuring transducers and meters will read higher than the user expects. The true RMS measuring transducer and/or meter are registering the correct RMS value of the applied voltage.
Customers ask, "How can I read the correct value of the applied voltage?" Well, they are reading the correct value.
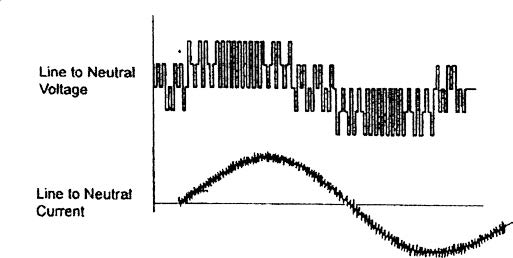
Figure 1. Voltage and current wave shapes produced by a typical frequency converter.
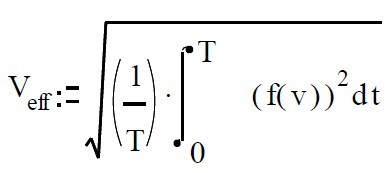
Figure 2. RMS Calculation of the voltage
f(v) is the function of the voltage for the RMS calculation. In the case of the frequency converter the voltage function consists of a series of voltage pulses of varying width that are both positive and negative. By squaring the pulses ([f(v)]2 ), all pulses (including negative swinging pulses interspersed with the positive swinging pulses and the positive swinging pulses interspersed with the negative swing pulses) contribute to the RMS value. As a result, the true RMS or effective voltage produced is higher than expected compared to the synthesized sine wave voltage envelope.
Measuring the Current
Because a motor load is inductive it filters out the high frequency component from the frequency converter and the current is observed as a sine wave with ripple. A true RMS measuring meter or transducer measures the effective current used by the motor load.
Measuring the Power
Because the synthesized voltage sine wave from the frequency converter may vary from near DC to some nominal AC frequency such as 66 hertz, power measurement devices must have a response from DC to the maximum expected synthesized frequency and must respond fast enough to capture the pulse width modulation frequency.
A properly designed power transducer will multiply the individual voltage pulses by the current and average the product over a sufficient time period to give a relatively smooth output.
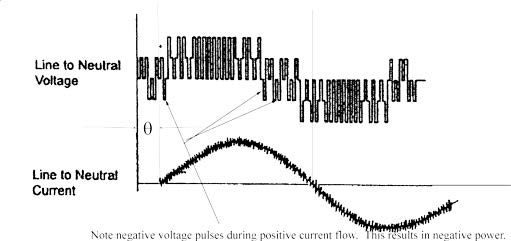
This is figure 1 again with some comments. θ is the angle by which the current lags the voltage — the power factor angle. This is indicative of an inductive load. Note the negative voltage pulses occurring while the current is positive. This results in negative power flow. Likewise note the positive voltage pulses occurring while the current is negative. This too results in negative power.
The power measured by the variable frequency power transducer reflects the power consumed by the motor developing shaft power, resistive losses that are normal with a motor, and the additional resistive losses as a result of the pulse width modulated voltage. As a result of the latter, an induction motor operating from a frequency converter will run a little hotter. To correct for this, some motor manufacturers specify using a reactor between the frequency converter and motor. The reactor is an inductor that will filter out the high frequency voltage pulses. Measuring the voltage between the reactor and the motor will give results closer to what one expects from a sine wave voltage. Measuring the power between the reactor and motor eliminates most of the power lost to heat as a result of the voltage PWM wave shape and thus more accurately measures shaft power.
Addressing the Problem of what the user really wants to Measure
Frequency converters as supplied today may provide a voltage output that is a nice clean sine wave or an unfiltered output with the carrier frequency. Carrier frequencies can range from a few kilohertz to as high as 30 kilohertz depending on the manufacturer. Please check with the manufacturer of the frequency converter that you are using. You should not have any measuring problems if:
These readings are not wrong but they do not reflect the work being done by the motor.What to do?
Solution 1
If the carrier frequency is in the kilohertz range
you might try adding a filter before the input to the voltage transducer and the watt transducer.A couple 0.2 mfd ceramic capacitors and a couple 100 ohm resistors wired as a pi network filter may work well filtering out the carrier.
Solution 2
Another approach is more sophisticated. Build a semi-custom monitoring package based on DSP technology. The firmware in this monitoring package determines the zero crossing of the synthesized sine wave and the envelope. From this it is able to calculate all parameters. Please contact us regarding this solution. Pricing is very reasonable.
Solution 3
This solution is a "cop-out" solution but very reasonable. If power is the primary concern, measure the power going into the frequency converter. This is considerably less expensive than measuring the variable frequency side. The frequency converter manufacturer should be able to give you an efficiency rating for the frequency converter. From this rating and the power reading, you can calculate the power output from the motor.
Measuring the Voltage
True RMS measuring transducers and meters will read higher than the user expects. The true RMS measuring transducer and/or meter are registering the correct RMS value of the applied voltage.
Customers ask, "How can I read the correct value of the applied voltage?" Well, they are reading the correct value.
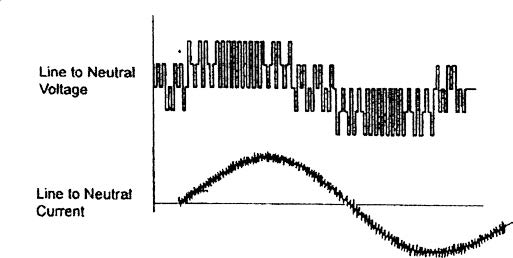
Figure 1. Voltage and current wave shapes produced by a typical frequency converter.
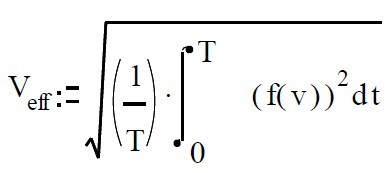
Figure 2. RMS Calculation of the voltage
f(v) is the function of the voltage for the RMS calculation. In the case of the frequency converter the voltage function consists of a series of voltage pulses of varying width that are both positive and negative. By squaring the pulses ([f(v)]2 ), all pulses (including negative swinging pulses interspersed with the positive swinging pulses and the positive swinging pulses interspersed with the negative swing pulses) contribute to the RMS value. As a result, the true RMS or effective voltage produced is higher than expected compared to the synthesized sine wave voltage envelope.
Measuring the Current
Because a motor load is inductive it filters out the high frequency component from the frequency converter and the current is observed as a sine wave with ripple. A true RMS measuring meter or transducer measures the effective current used by the motor load.
Measuring the Power
Because the synthesized voltage sine wave from the frequency converter may vary from near DC to some nominal AC frequency such as 66 hertz, power measurement devices must have a response from DC to the maximum expected synthesized frequency and must respond fast enough to capture the pulse width modulation frequency.
A properly designed power transducer will multiply the individual voltage pulses by the current and average the product over a sufficient time period to give a relatively smooth output.
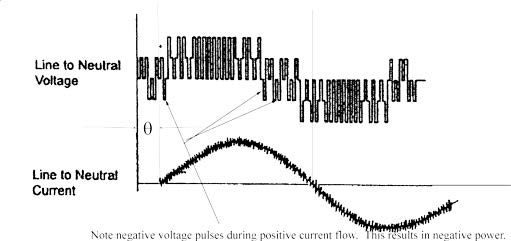
This is figure 1 again with some comments. θ is the angle by which the current lags the voltage — the power factor angle. This is indicative of an inductive load. Note the negative voltage pulses occurring while the current is positive. This results in negative power flow. Likewise note the positive voltage pulses occurring while the current is negative. This too results in negative power.
The power measured by the variable frequency power transducer reflects the power consumed by the motor developing shaft power, resistive losses that are normal with a motor, and the additional resistive losses as a result of the pulse width modulated voltage. As a result of the latter, an induction motor operating from a frequency converter will run a little hotter. To correct for this, some motor manufacturers specify using a reactor between the frequency converter and motor. The reactor is an inductor that will filter out the high frequency voltage pulses. Measuring the voltage between the reactor and the motor will give results closer to what one expects from a sine wave voltage. Measuring the power between the reactor and motor eliminates most of the power lost to heat as a result of the voltage PWM wave shape and thus more accurately measures shaft power.
Addressing the Problem of what the user really wants to Measure
Frequency converters as supplied today may provide a voltage output that is a nice clean sine wave or an unfiltered output with the carrier frequency. Carrier frequencies can range from a few kilohertz to as high as 30 kilohertz depending on the manufacturer. Please check with the manufacturer of the frequency converter that you are using. You should not have any measuring problems if:
- The frequency converter output is well filtered.
- There is a reactor between the frequency converter and your motor. Connect your transducers or instruments between the reactor and the motor.
These readings are not wrong but they do not reflect the work being done by the motor.What to do?
Solution 1
If the carrier frequency is in the kilohertz range
you might try adding a filter before the input to the voltage transducer and the watt transducer.A couple 0.2 mfd ceramic capacitors and a couple 100 ohm resistors wired as a pi network filter may work well filtering out the carrier.
Solution 2
Another approach is more sophisticated. Build a semi-custom monitoring package based on DSP technology. The firmware in this monitoring package determines the zero crossing of the synthesized sine wave and the envelope. From this it is able to calculate all parameters. Please contact us regarding this solution. Pricing is very reasonable.
Solution 3
This solution is a "cop-out" solution but very reasonable. If power is the primary concern, measure the power going into the frequency converter. This is considerably less expensive than measuring the variable frequency side. The frequency converter manufacturer should be able to give you an efficiency rating for the frequency converter. From this rating and the power reading, you can calculate the power output from the motor.
Post a Comment:
You may also like: