Category
- Products
- FAQ
- Contact us
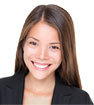
Frequency inverter manufacturers
Home » Application » Frequency inverter for blast blower
Frequency inverter for blast blower
A Coking Plant has 2 sets of 58 model coking furnace, 1 set of 80 coking furnace and related spare coal and gas as well as completed production system including purifying, chemical material collecting and sewage treatment system. The plant produces carbon coke 1120000t, coking coal gas 500 million m3, tar oil 45000t, crude benzol 13000t and ammonium sulfate 15000t in a year with daily sewage treatment 2400t.
With carbon coke production increasing, coal gas collection is increasing. Original operation mode of "one work, two standby" does not meet production requirement in summer. Because increasing pressure and temperature can not discharge outside in time, it may cause explosion. In production technics of coking furnace, control effect of coal gas pressure affects production directly. Higher pressure inside furnace causes black smoke from coking furnace. Coal gas leakage pollutes environment and it is harmful to workers health. Lower pressure leads to negative pressure operation, suck much air and waste much coal gas. That affects production and quality of carbon coke and coal gas heavily. Long term of negative pressure operation will affect normal production and lifetime of coking furnace.
If blast blower works in "two work, one standby", main pipe pressure is controlled by return valve. Because pressure difference is big, it causes intense vibration of main pipe pressure when adjustment valve acts gently. This method can not meet technics requirement. It would lead to big change of coal gas pressure and coal gas needed, causing insufficient coal gas or abnormal production for outside user. Coal gas return flow also wastes energy. After full investigations, the plant decided to use frequency inverter to control speed, thereby adjusting pipe pressure.
Scheme design
1. Electric design
The plant has 3 sets of D1350-1.237/0.887 coal gas blast blower. They usually work in "one work, two standby", only in "two work, one standby" for summer. According to actual state, plant choose the frequency inverter "one drive one" and "one drive two".
1.1 Main circuit principle
Take 1# blower for example: circuit is composed of 3 contactors KM11, KM12, KM13 and 2 medium voltage isolators QS11, QS12. Contactors are used to switch variable frequency and direct on line. Isolators are always closed and only open for frequency inverter maintenance. Main circuit of 3# and 4# blower is similar.
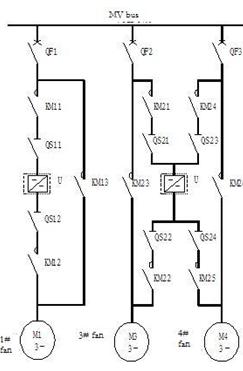
Characters:
a. Switch between direct on line and variable frequency state automatically. When frequency inverter is broken, system can switch into direct on line automatically. When user stops frequency inverter, no need to stop load.
b. Implement "one work, two standby" and "two work, one standby" easily. Namely one works in variable frequency state, one standby in variable frequency, one standby in direct on line; two work in variable frequency, one standby in direct on line.
1.2 The frequency inverter adopts technology of cell-cascade multi-level voltage source topology.
Its advantages: input multiple design makes less harmonic. Cell-cascade output makes low harmonic. Without output filter, THD<0.3%. It can be called as "perfect harmonic" frequency inverter. Lower torque vibration and motor noise. Power factor can reach 0.95. No damage on motor insulation and no limitation on cable length. It is convenient for redundancy design.
1. Automatization network design
Control system is composed of main control PLC, bypass control PLC, frequency inverter and upper PC. Main control is Siemens S7-300PLC, bypass control is S7-200-PLC. Communication network adopts Profibus DP in bottom. Main control and upper PC adopt ethernet communication. As control center of whole system, S7-300PLC copes with kinds of requirements from HMI. It monitors parameters of whole system, implements PID regulation for pipe pressure and keeps pipe pressure constant. S7-200PLC of auto bypass switches between variable frequency and direct on line. Upper PC connects to PLC by ethernet. Take account of high requirement for safety, reliability and stability, we use Profibus DP for site control and ethernet for monitor operation. Connect it to master server of local area network in coking plant, and implement remote monitor. Siemens S7-200 equips with EM277 Profibus module; S7-300 uses 315-2 DP and equips with CP341-1T ethernet module, DP terminal is used to connect S7-200,ethernet module CP343-1T is used to connect ethernet of upper PC.
Control network has these characters: excellent stability, expansibility, exploration of hardware/software and friendly man-machine interface as well as advantage of redundancy design of upper PC.
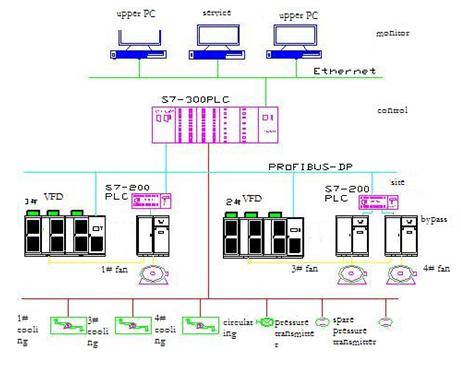
3. Software design
Software of upper PC has friendly man-machine interface. It supports ethernet, kinds of PLC communication and OPC, and remote monitor easily. It has functions of report and alarm.
Because upper PC programme does not support ethernet communication protocol of Siemens, it needs OPC Server as transition. This way makes machine of local area network invokes parameter of this computer conveniently. That is advantageous for remote monitor.
S7-300 PLC adopts Step 7 to make programme. Adopting module programme mode, software programs function part for each work in one OB to invoke.That is easy for user to understand and change. It supports ladder drawing and statement list. It also adopts failure-tolerant programme design to intensify system stability.
4. Control design
4.1 Self-start control of oil route cooling
Hydraulic oil pump should start before starting blast blower every time to make oil flow to increase in order to cool heat resulted from friction. Otherwise blast blower can not be started. During operation, if master oil pump can not meet requirement, auxiliary oil pump starts and heat according to oil temperature automatically. Furthermore, it inspects for block state of oil route and oil temperature of different points.
4.2 Auto switch of variable frequency and direct on line
During variable frequency operation, if frequency inverter is broken, system switches to direct on line automatically. At the same time, small circulating return valve opens immediately. Coal gas pressure is controlled by return valve. Small circulating opening is set at 50% to ensure undisturbed switch.
4.3 Undisturbed switch of two blast blowers
For 1# unit, if its frequency inverter or blower needs to stop and maintenance, user switches 3# unit. First, start 3# blower by 2# frequency inverter, at the same time, stop 1# frequency inverter. PID close loop control of pressure makes 1# stop smoothly as per deceleration time. Inlet flow reduces slowly. In contrast, 3# blower accelerates as per acceleration time. Speed rises smoothly, inlet flow increases slowly. This way can ensure main pipe pressure constant and implement undisturbed switch of two blowers. It avoids intense pressure vibration resulted from switch of two blowers in original system.
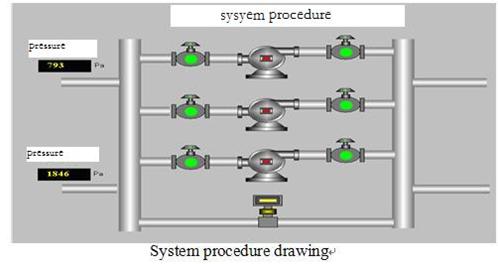
4.4 Pressure PID close loop control
For parameters such as pressure and flow, object adjustment route time constant T0 is small, but load changes quickly. At the moment, integral and differential all cause vibration, affecting adjustment quality greatly. So differential adjustment law should be not adopted. Auto adjustment of coal gas pressure and small circulating valve all adopt PI adjustment. The more P is, the stronger proportional adjustment is; the less I is, the stronger integral is.
4.5 Pressure transmitter failure control
For some control systems with requirement of high reliability, object controlled puts forward multi-sampling theory. So sample two pressure points at main pipe. Send pressure values of these two points to PLC S7-300 to compare. If difference value is bigger than some value, pressure transmitter with smaller value is judged as the fault. In this way, it guarantees sample pressure accuracy and thereby ensures system reliability.
4.6 Emergency fault measure
Variable frequency system has emergency operation box in central control room. In the case of control system paralysis, act switch, break off contactors by hard wire, start motor in direct on line. For example, Profibus cable is broken, blower is out of control. Pressure reduces slowly due to blower inertia. At the moment, control system alarms and reports communication fault. It needs quick manual intervention to switch to original control mode.
4.7 Heat redundancy control of two upper PCs
Two upper PCs monitor whole system simultaneously. When master PC is broken and exits, slave PC can monitor system. So system safety and reliability is ensured.
Conclusion
Controlling blast blower by frequency inverter maintains constant pressure of main pipe. It improves coking furnace production and site environment, meets technics requirement completely. Integration of PLC control, PROFIBUS technology and frequency inverter makes high automatization level, reliable work, easy operation and considerable energy saving. It solves that return valve can not implement constant pressure and undisturbed switch when two blowers run in parallel, which is always a puzzle for coking furnace production.
The successful application of frequency inverter in blast blower has enormous economic value for improving environment, heightening return and quality of coal gas. So it is worthy to expand and promote widely.
With carbon coke production increasing, coal gas collection is increasing. Original operation mode of "one work, two standby" does not meet production requirement in summer. Because increasing pressure and temperature can not discharge outside in time, it may cause explosion. In production technics of coking furnace, control effect of coal gas pressure affects production directly. Higher pressure inside furnace causes black smoke from coking furnace. Coal gas leakage pollutes environment and it is harmful to workers health. Lower pressure leads to negative pressure operation, suck much air and waste much coal gas. That affects production and quality of carbon coke and coal gas heavily. Long term of negative pressure operation will affect normal production and lifetime of coking furnace.
If blast blower works in "two work, one standby", main pipe pressure is controlled by return valve. Because pressure difference is big, it causes intense vibration of main pipe pressure when adjustment valve acts gently. This method can not meet technics requirement. It would lead to big change of coal gas pressure and coal gas needed, causing insufficient coal gas or abnormal production for outside user. Coal gas return flow also wastes energy. After full investigations, the plant decided to use frequency inverter to control speed, thereby adjusting pipe pressure.
Scheme design
1. Electric design
The plant has 3 sets of D1350-1.237/0.887 coal gas blast blower. They usually work in "one work, two standby", only in "two work, one standby" for summer. According to actual state, plant choose the frequency inverter "one drive one" and "one drive two".
1.1 Main circuit principle
Take 1# blower for example: circuit is composed of 3 contactors KM11, KM12, KM13 and 2 medium voltage isolators QS11, QS12. Contactors are used to switch variable frequency and direct on line. Isolators are always closed and only open for frequency inverter maintenance. Main circuit of 3# and 4# blower is similar.
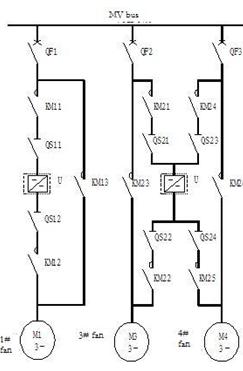
Characters:
a. Switch between direct on line and variable frequency state automatically. When frequency inverter is broken, system can switch into direct on line automatically. When user stops frequency inverter, no need to stop load.
b. Implement "one work, two standby" and "two work, one standby" easily. Namely one works in variable frequency state, one standby in variable frequency, one standby in direct on line; two work in variable frequency, one standby in direct on line.
1.2 The frequency inverter adopts technology of cell-cascade multi-level voltage source topology.
Its advantages: input multiple design makes less harmonic. Cell-cascade output makes low harmonic. Without output filter, THD<0.3%. It can be called as "perfect harmonic" frequency inverter. Lower torque vibration and motor noise. Power factor can reach 0.95. No damage on motor insulation and no limitation on cable length. It is convenient for redundancy design.
1. Automatization network design
Control system is composed of main control PLC, bypass control PLC, frequency inverter and upper PC. Main control is Siemens S7-300PLC, bypass control is S7-200-PLC. Communication network adopts Profibus DP in bottom. Main control and upper PC adopt ethernet communication. As control center of whole system, S7-300PLC copes with kinds of requirements from HMI. It monitors parameters of whole system, implements PID regulation for pipe pressure and keeps pipe pressure constant. S7-200PLC of auto bypass switches between variable frequency and direct on line. Upper PC connects to PLC by ethernet. Take account of high requirement for safety, reliability and stability, we use Profibus DP for site control and ethernet for monitor operation. Connect it to master server of local area network in coking plant, and implement remote monitor. Siemens S7-200 equips with EM277 Profibus module; S7-300 uses 315-2 DP and equips with CP341-1T ethernet module, DP terminal is used to connect S7-200,ethernet module CP343-1T is used to connect ethernet of upper PC.
Control network has these characters: excellent stability, expansibility, exploration of hardware/software and friendly man-machine interface as well as advantage of redundancy design of upper PC.
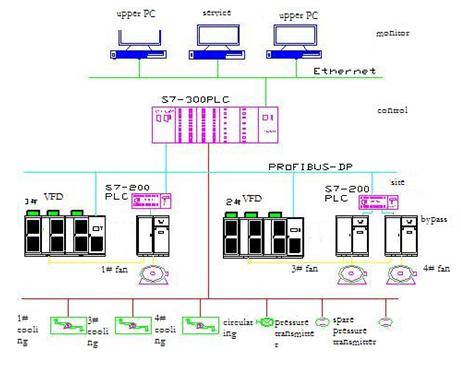
3. Software design
Software of upper PC has friendly man-machine interface. It supports ethernet, kinds of PLC communication and OPC, and remote monitor easily. It has functions of report and alarm.
Because upper PC programme does not support ethernet communication protocol of Siemens, it needs OPC Server as transition. This way makes machine of local area network invokes parameter of this computer conveniently. That is advantageous for remote monitor.
S7-300 PLC adopts Step 7 to make programme. Adopting module programme mode, software programs function part for each work in one OB to invoke.That is easy for user to understand and change. It supports ladder drawing and statement list. It also adopts failure-tolerant programme design to intensify system stability.
4. Control design
4.1 Self-start control of oil route cooling
Hydraulic oil pump should start before starting blast blower every time to make oil flow to increase in order to cool heat resulted from friction. Otherwise blast blower can not be started. During operation, if master oil pump can not meet requirement, auxiliary oil pump starts and heat according to oil temperature automatically. Furthermore, it inspects for block state of oil route and oil temperature of different points.
4.2 Auto switch of variable frequency and direct on line
During variable frequency operation, if frequency inverter is broken, system switches to direct on line automatically. At the same time, small circulating return valve opens immediately. Coal gas pressure is controlled by return valve. Small circulating opening is set at 50% to ensure undisturbed switch.
4.3 Undisturbed switch of two blast blowers
For 1# unit, if its frequency inverter or blower needs to stop and maintenance, user switches 3# unit. First, start 3# blower by 2# frequency inverter, at the same time, stop 1# frequency inverter. PID close loop control of pressure makes 1# stop smoothly as per deceleration time. Inlet flow reduces slowly. In contrast, 3# blower accelerates as per acceleration time. Speed rises smoothly, inlet flow increases slowly. This way can ensure main pipe pressure constant and implement undisturbed switch of two blowers. It avoids intense pressure vibration resulted from switch of two blowers in original system.
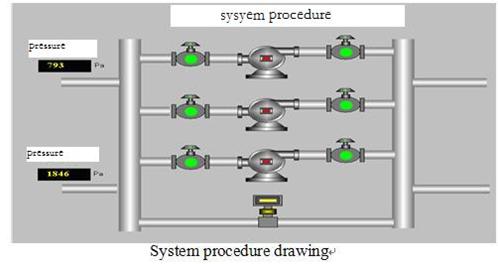
4.4 Pressure PID close loop control
For parameters such as pressure and flow, object adjustment route time constant T0 is small, but load changes quickly. At the moment, integral and differential all cause vibration, affecting adjustment quality greatly. So differential adjustment law should be not adopted. Auto adjustment of coal gas pressure and small circulating valve all adopt PI adjustment. The more P is, the stronger proportional adjustment is; the less I is, the stronger integral is.
4.5 Pressure transmitter failure control
For some control systems with requirement of high reliability, object controlled puts forward multi-sampling theory. So sample two pressure points at main pipe. Send pressure values of these two points to PLC S7-300 to compare. If difference value is bigger than some value, pressure transmitter with smaller value is judged as the fault. In this way, it guarantees sample pressure accuracy and thereby ensures system reliability.
4.6 Emergency fault measure
Variable frequency system has emergency operation box in central control room. In the case of control system paralysis, act switch, break off contactors by hard wire, start motor in direct on line. For example, Profibus cable is broken, blower is out of control. Pressure reduces slowly due to blower inertia. At the moment, control system alarms and reports communication fault. It needs quick manual intervention to switch to original control mode.
4.7 Heat redundancy control of two upper PCs
Two upper PCs monitor whole system simultaneously. When master PC is broken and exits, slave PC can monitor system. So system safety and reliability is ensured.
Conclusion
Controlling blast blower by frequency inverter maintains constant pressure of main pipe. It improves coking furnace production and site environment, meets technics requirement completely. Integration of PLC control, PROFIBUS technology and frequency inverter makes high automatization level, reliable work, easy operation and considerable energy saving. It solves that return valve can not implement constant pressure and undisturbed switch when two blowers run in parallel, which is always a puzzle for coking furnace production.
The successful application of frequency inverter in blast blower has enormous economic value for improving environment, heightening return and quality of coal gas. So it is worthy to expand and promote widely.
Post a Comment:
You may also like: