Category
- Products
- FAQ
- Contact us
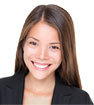
Frequency inverter manufacturers
Home » Application » Frequency inverter for ID fan in mining industry
Frequency inverter for ID fan in mining industry
In most middle/large mining companies, power consumption of motor accounts for 50% of total power consumption. LV frequency inverter is very common. But, defectiveness of MV variable frequency technology, and voltage withstand capacity of components have been restricting MV frequency inverter development and its application. In recent years, with rapid development of MV technology and voltage withstand function, MV frequency inverter has been used widely. Its energy saving effect is considerable.
Introduction
There were 4 low voltage motors (315kW, 562A, 1476r/min) in flue gas purification system. In general, 2~3 motors worked and another was spare. Fans connected in parallel. Subpressure was controlled by valve. Valve opening was controlled just by personnel experience. In 2005, plant decided to reform purification system with medium voltage frequency inverter. Mode of one work and one spare was suggested to ensure safety and reliability.
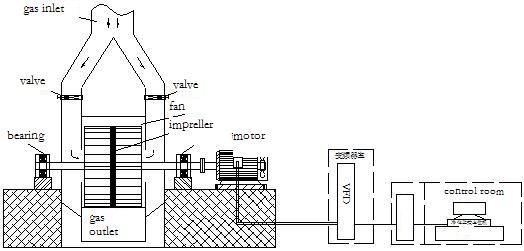
Fig1: purification system layout drawing
1. Driving equipments
MV asynchronous motor: 1000kW, 50Hz , Ve=6300V, Ie=108.95A; ne=994r/min; cosφ=0.876, insulation class: F, connecting: Y, allowed to start once in hot state and twice in cold state.
2. Centrifugal ID fan
338600m3/h; 7500Pa; ne=990r/min; 1000kW.
The frequency inverter adopts technology of cell-cascaded, high-medium voltage source, 6kV input. Medium voltage is transferred to low voltage through transformer. Then it goes through diode and IGBT inverter. Then cells cascaded output 6.3kV.
Fig 3:6kV frequency inverter system drawing
Benefits
The frequency inverter has been running stably in flue gas purification system for 3 years since August, 2008. System also runs healthily. Energy saving is considerable and achieves expected goal. It also meets technology requirement and improves purification effect, which makes plant be prized by local environmental protection bureau. According to related statistics, power consumption of purification system has been down 19%. Actual data is in following:
Conclusion
Frequency inverter application in purification system optimizes the system performance, improves purification effect, reduces power consumption greatly. According to related statistic, flue gas consumption reduces 19m3/t. Total power consumption reduces 137000kW.h per month.
Introduction
There were 4 low voltage motors (315kW, 562A, 1476r/min) in flue gas purification system. In general, 2~3 motors worked and another was spare. Fans connected in parallel. Subpressure was controlled by valve. Valve opening was controlled just by personnel experience. In 2005, plant decided to reform purification system with medium voltage frequency inverter. Mode of one work and one spare was suggested to ensure safety and reliability.
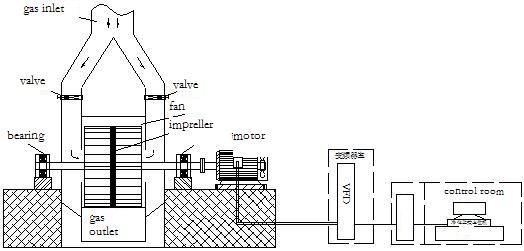
Fig1: purification system layout drawing
1. Driving equipments
MV asynchronous motor: 1000kW, 50Hz , Ve=6300V, Ie=108.95A; ne=994r/min; cosφ=0.876, insulation class: F, connecting: Y, allowed to start once in hot state and twice in cold state.
2. Centrifugal ID fan
338600m3/h; 7500Pa; ne=990r/min; 1000kW.
Frequency inverter structure and working principle
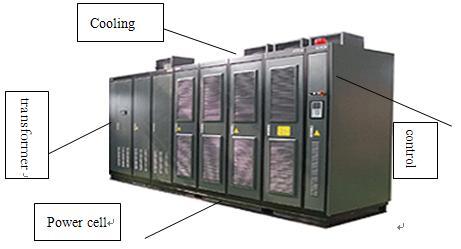
The frequency inverter adopts technology of cell-cascaded, high-medium voltage source, 6kV input. Medium voltage is transferred to low voltage through transformer. Then it goes through diode and IGBT inverter. Then cells cascaded output 6.3kV.
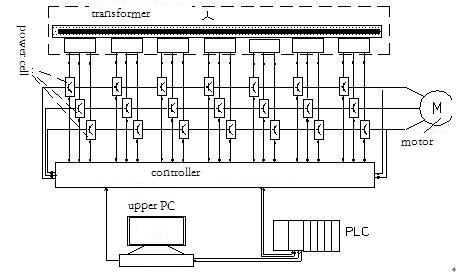
Fig 3:6kV frequency inverter system drawing
Benefits
The frequency inverter has been running stably in flue gas purification system for 3 years since August, 2008. System also runs healthily. Energy saving is considerable and achieves expected goal. It also meets technology requirement and improves purification effect, which makes plant be prized by local environmental protection bureau. According to related statistics, power consumption of purification system has been down 19%. Actual data is in following:
NO | Furnace | Subpressure (Pa) | Frequency (Hz) | Current (A) | Result | Remark |
1 | 1system | 960—1020 | 19 | 26 | Up to standard |
|
2 | 2 systems | 1000—1100 | 24 | 34 | Up to standard | |
3 | 3 systems | 1050—1150 | 27 | 41 | Up to standard | |
4 | 4 systems | 1100—1200 | 31 | 47 | Up to standard | |
5 | 5 systems | 1160—1250 | 35 | 52 | Up to standard | |
6 | 6 systems | 1200—1130 | 38 | 58 | Up to standard |
Conclusion
Frequency inverter application in purification system optimizes the system performance, improves purification effect, reduces power consumption greatly. According to related statistic, flue gas consumption reduces 19m3/t. Total power consumption reduces 137000kW.h per month.
Post a Comment:
You may also like: