Category
- Products
- FAQ
- Contact us
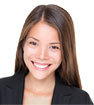
Frequency inverter manufacturers
Home » Application » Frequency inverter for pump protection
Frequency inverter for pump protection
In our gas plant we pump natural gas liquids with a double-suction high-speed centrifugal pump. It runs with a discharge pressure of 60 Barg at 6,700 rpm, and is designed for a flow rate of 670 m3/hr. A booster pump discharges at 20 Barg to the natural gas liquids pump suction. The natural gas liquids, which has a specific gravity of 0.52, then travels about 400 km to our refinery for fractionation. About 35–40% of the pumped fluid recycles into the surge bullet via a recycle valve, wasting energy. There are other problems: vibration trips in low flow due to shaft deflections, seal leaks, etc. So, we're planning to buy a new pump, preferably one that will allow us to save energy and avoid such problems. What type of pump do you consider the best choice for this application?
Energy Efficiency Design
The booster pump and the export pump should have their own minimum-flow recycle valves. These minimum flows need to be maintained at all times -- either by a flow control valve or a restrictive orifice. A restrictive orifice is simpler; however, it will waste energy. I suggest flow control loops so that the flow is recycled only when needed. If flow above the minimum rate is required and the economics allow, use frequency inverters to reduce energy consumption.
The problems reported may be due to low seal pressure. Double mechanical seals require pressure above the pump discharge pressure. Otherwise, hydrocarbon will migrate to the seal system. Another symptom -- pump vibration at low flow -- may be due to improper alignment and cavitation. The same problems will appear with the new pump if the cause is not clearly established.
Reduce the Shaft Speed
I think the problems can be divided into two categories -- design and operational.
The high rotational speed of these pumps causes overheating at the seal faces and seal failure. The high peripheral velocities are too close to the manufacturer's design limits. Another design problem is shaft deflection, which is highest at low flow. Under these conditions, high radial forces, created by the high pressure in the pump casing, act on the shaft and impeller. The pump's double volutes are ineffective. As a result, the pumps vibrate severely, enough to cause tripping. Operationally, the pump wastes energy because of the high recycle flow.
I suggest exploring:
Although a frequency converter on a single pump may seem to be the answer, it is not. The natural gas liquids pump will still be operating far below the BEP. Shaft vibration at low flow with high speed pumps is a fairly common occurrence. The problem is less about the speed than hydraulic efficiency. Consider two smaller pumps operating in tandem, fed by the booster pump. You may want to improve efficiency with a frequency converter on the lead pump but that's fine-tuning the solution. With smaller pumps, you can probably get closer to the BEP, at least at maximum capacity, i.e., with both pumps operating. Smaller pumps mean lower minimum flow and less energy inefficiency.
We used an old welded stainless steel silo at our site to store dried brewers grain. During a September shutdown, we installed a new bagger and weigh scale. This prevented us from loading railcars for several days. So, to keep the dryer running during the outage, we cut its output to a rate that would only fill up the silo. The weather was hot but a rainstorm swept through with a cold front. After the storm, we noticed a seam on the silo had split apart, dumping several hundred tons of dried brewers grain. Now, corporate managers, concerned because another plant is planning a similar shutdown and bagger installation soon, want to know why the silo failed. What do you think caused the accident? What should we tell management?
Energy Efficiency Design
The booster pump and the export pump should have their own minimum-flow recycle valves. These minimum flows need to be maintained at all times -- either by a flow control valve or a restrictive orifice. A restrictive orifice is simpler; however, it will waste energy. I suggest flow control loops so that the flow is recycled only when needed. If flow above the minimum rate is required and the economics allow, use frequency inverters to reduce energy consumption.
The problems reported may be due to low seal pressure. Double mechanical seals require pressure above the pump discharge pressure. Otherwise, hydrocarbon will migrate to the seal system. Another symptom -- pump vibration at low flow -- may be due to improper alignment and cavitation. The same problems will appear with the new pump if the cause is not clearly established.
Reduce the Shaft Speed
I think the problems can be divided into two categories -- design and operational.
The high rotational speed of these pumps causes overheating at the seal faces and seal failure. The high peripheral velocities are too close to the manufacturer's design limits. Another design problem is shaft deflection, which is highest at low flow. Under these conditions, high radial forces, created by the high pressure in the pump casing, act on the shaft and impeller. The pump's double volutes are ineffective. As a result, the pumps vibrate severely, enough to cause tripping. Operationally, the pump wastes energy because of the high recycle flow.
I suggest exploring:
- A lower capacity impeller. Design for the identical head with increased shaft stiffness and reduced throat bushing clearances. The material of construction may need to be changed. These modifications should reduce low-flow vibration.
- A two-pole motor, constant speed direct-drive.
- A multi-stage pump. It offers many advantages over a single-stage pump, including: a lower shaft speed, resulting in increased life of bearings and seals; reduced shaft deflection; elimination of a speed-increaser gear box, reducing energy consumption; and less motor horsepower.
Although a frequency converter on a single pump may seem to be the answer, it is not. The natural gas liquids pump will still be operating far below the BEP. Shaft vibration at low flow with high speed pumps is a fairly common occurrence. The problem is less about the speed than hydraulic efficiency. Consider two smaller pumps operating in tandem, fed by the booster pump. You may want to improve efficiency with a frequency converter on the lead pump but that's fine-tuning the solution. With smaller pumps, you can probably get closer to the BEP, at least at maximum capacity, i.e., with both pumps operating. Smaller pumps mean lower minimum flow and less energy inefficiency.
We used an old welded stainless steel silo at our site to store dried brewers grain. During a September shutdown, we installed a new bagger and weigh scale. This prevented us from loading railcars for several days. So, to keep the dryer running during the outage, we cut its output to a rate that would only fill up the silo. The weather was hot but a rainstorm swept through with a cold front. After the storm, we noticed a seam on the silo had split apart, dumping several hundred tons of dried brewers grain. Now, corporate managers, concerned because another plant is planning a similar shutdown and bagger installation soon, want to know why the silo failed. What do you think caused the accident? What should we tell management?
Post a Comment:
You may also like: