Category
- Products
- FAQ
- Contact us
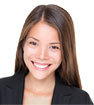
Frequency inverter manufacturers
Home » Application » Frequency inverter in Steel & Iron industry
Frequency inverter in Steel & Iron industry
Motor application is very widely used in all industries. It is main power in enterprise and drives equipment, such as fan, milling and pump in metallurgy, oil, power and mining. Power consumption of medium voltage motor is enormous, accounting for 65~75%. In term of energy saving for motor, technology of variable frequency is the best way for speed adjustment, start-up and stop. Particular in some special technologies, energy saving effect of frequency inverter is more obvious.
Frequency inverter classification
There are several types: star/delta starter; auto-transformer start-up; capacitor compensator; electromagnetism speed adjustor (stepless speed adjustment). Energy saving of all above speed adjustment methods is not obvious. Furthermore, adjustment range is small, speed is unstable, motor efficiency is low. There is big loss, frequent fault, low precision and slow response, which can not meet requirement of production continuity. Original adjustment method is valve opening control. In this method, input power is big and much energy is wasted on damper. For frequency inverter, it controls flow by changing speed.
According to fluid mechanics, P(power)=Q(flow)×H(pressure), we know Q is in direct rate to N(speed), H is in direct rate to square of N, P is in direct rate to cube of N. If efficiency of fan/pump is fixed, when flow is required to reduce, N can reduce proportionally, output shaft power reduces in cube. Namely power consumption of fan/pump is nearly in cube relationship with speed. When flow is required to lower, frequency inverter adjusts frequency to make motor speed lower proportionally. So motor power reduces in cube, which saves energy 40%~50% in contrast to damper/valve control mode.
Case analysis
Take example of the frequency inverter which put into service in dusting fan of a Steel & Iron Company in 2006.
Technologies
During production of blast furnace, there is much gas. According to state law, it needs treatment.
Dusting fan work is intermittent. It works when furnace outputs iron and does not work when no iron output. Utilization rate is about 60%. Following is technologies drawing:
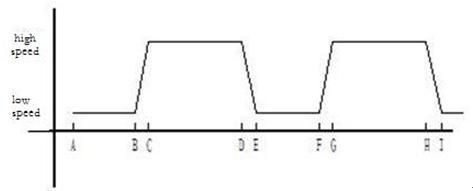
A~B, E~F: refining time
B~C, F~G: acceleration
C~D, G~H: output iron
D~E, H~I: deceleration
Output iron is 50min, it is high speed, set frequency 45Hz, adjustable.
Refining is 30min, it is low speed, set frequency 5Hz, adjustable.
Scheme
According to above technologies, motor can not stop frequently. In valve opening control mode, much energy is wasted on damper. In hydraulic coupling control, there are following disadvantages:
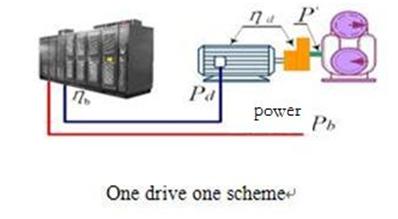
Character curve of dusting fan is following:
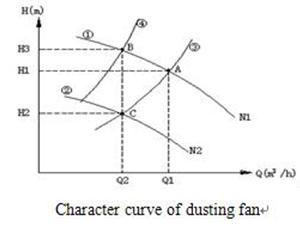
① is curve of running at speed N1, ② is curve of running at N2, ③④ is resistance curve of pipe network. In first load state, load works at A, flow is Q1, pressure is H1. If load still works at constant speed of N1, flow is adjusted to Q2 by damper, pressure will rise to H3, work point moves to B. Resistance curve of pipe network changes to④ from ③.
At A and B, load power: PA=H1×Q1, PB=H3×Q2. Q2<Q1, but H3>H1, actual power reducing is limited.
If adjustment does not adopt damper control, resistance curve ③ does not change. Reduce flow by adjusting load speed, load runs at speed N2, work curve is ②. Load works at C, flow is still Q2, pressure is H2.
Compare B and C, shaft power reducing is: ΔP=PB- PC=(H3–H2)×Q2
In the case of resistance character unchanging, there is relationship between centrifugal fan flow Q, pressure H, shaft power P and speed N:
Q∝N, H∝N2,P∝N3
So,

That is to say, in variable frequency adjustment, in the case of taking no account of efficiency, when flow reduces to half, shaft power of fan lowers 87.5%. This is the reason why frequency inverter has such considerable energy saving effect on fans.
In addition, starting in direct on line brings big impact on power grid and mechanism as well as big noise. Estimation loss of each start-up: Ws=0.5Jwo²(1+r1/r2)Tm/Tm-TL. Square torque character of fan is similar to mechanism character of asynchronous motor in starting, so Tm/Tm-TL=1. But in frequency inverter control, soft start makes start loss small, only 10% of Ws. Therefore, energy saving of start-up is very considerable.
In frequency inverter control, because filter capacitor inside frequency inverter improves power factor, power factor is near to 1 at 50Hz. Work current is far less than rated current. It can save 20% capacity for power grid.
Operation effect
Parameters of 6# dusting fan:
Rated power 710kW, rated voltage 6kV, rated current 89A, power factor 0.816, rated speed 740r/min.
Frequency inverter input values:
High speed (45Hz), current 50~55A; low speed (5Hz), current 1.36A. According to formula: frequency inverter input voltage U1×frequency inverter input current I1×frequency inverter power factor=frequency inverter output voltageU2×industry frequency current I2×motor power factor. Actual operation industry frequency current is: high speed 59~65A, low speed 18A.
In high speed, input current 55A, input voltage 6450V, speed 740r/min;
In low speed, input current 1.3A, input voltage 540V, speed 76r/min.
Make calculation as per frequency inverter display values. Output iron time and non output time rate is 60% and 40%. Yearly work time is 8000h.
In direct on line state, power consumption is
√3 ×Ue×I×cosΦ=1.732×6.450×65×0.816=592.5kW·h
Power cost: 0.5yuan/kW.h, 592.5×8000×0.5=2370124 yuan
In variable frequency state, speed is in direct rate to frequency, relationship of power and speed is:
P/Pe= (n/ne)3
In high speed: P=Pe× (n/ne)3/0.96=739.5kW·h
Power cost: 739.5× (8000×60%)×0.5=1774800 yuan
In low speed: P=Pe× (n/ne)3/0.96=0.74 kW·h
Power cost: 0.74× (8000×40%)×0.5=1184 yuan
Yearly cost saved: 2370124-1774800-1184=594140 yuan (USD 87373). Energy saving rate is 25%. Cost can be repaid in one and half year.
Other benefits of using frequency inverter:
a. Less maintenance
Generally, main purpose of frequency inverter application is to reduce motor speed. Slow start-up and low speed prolong equipment lifetime and reduce impact on pipe. Maintenance period of pipe is reduced and maintenance cost is saved.
b. Less work labour
Variable frequency system adopts computer interlock control between running equipment and standby equipment. System implements automatic operation and related protection and alarm. Work is changed to monitor work from manual work, which makes unmanned operation a reality. It lowers work labor greatly and heightens efficiency, ensures perfect operation.
c. Less impact on grid
With frequency inverter, system implements soft start. Start current is far less than rated current. Start-up time is prolonged, no big impact on power grid. It reduces mechanical damage on motor and prolongs equipment lifetime effectively.
Conclusion
Frequency inverter connects between power source and motor. It is replacing other speed adjustment drives and entering into kinds of industries rapidly as its safety and reliability. Its main purpose is to reduce equipment speed. It heightens automatization level, meets requirement of production technologies as well as energy saving. Furthermore, frequency inverter reduces maintenance cost greatly and brings considerable economic benefits for company. Frequency inverter plays an important role in energy saving of motor system.
Frequency inverter classification
There are several types: star/delta starter; auto-transformer start-up; capacitor compensator; electromagnetism speed adjustor (stepless speed adjustment). Energy saving of all above speed adjustment methods is not obvious. Furthermore, adjustment range is small, speed is unstable, motor efficiency is low. There is big loss, frequent fault, low precision and slow response, which can not meet requirement of production continuity. Original adjustment method is valve opening control. In this method, input power is big and much energy is wasted on damper. For frequency inverter, it controls flow by changing speed.
According to fluid mechanics, P(power)=Q(flow)×H(pressure), we know Q is in direct rate to N(speed), H is in direct rate to square of N, P is in direct rate to cube of N. If efficiency of fan/pump is fixed, when flow is required to reduce, N can reduce proportionally, output shaft power reduces in cube. Namely power consumption of fan/pump is nearly in cube relationship with speed. When flow is required to lower, frequency inverter adjusts frequency to make motor speed lower proportionally. So motor power reduces in cube, which saves energy 40%~50% in contrast to damper/valve control mode.
Case analysis
Take example of the frequency inverter which put into service in dusting fan of a Steel & Iron Company in 2006.
Technologies
During production of blast furnace, there is much gas. According to state law, it needs treatment.
Dusting fan work is intermittent. It works when furnace outputs iron and does not work when no iron output. Utilization rate is about 60%. Following is technologies drawing:
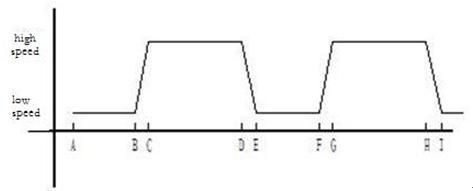
A~B, E~F: refining time
B~C, F~G: acceleration
C~D, G~H: output iron
D~E, H~I: deceleration
Output iron is 50min, it is high speed, set frequency 45Hz, adjustable.
Refining is 30min, it is low speed, set frequency 5Hz, adjustable.
Scheme
According to above technologies, motor can not stop frequently. In valve opening control mode, much energy is wasted on damper. In hydraulic coupling control, there are following disadvantages:
- Adjustment range is limited, about 50~95%. Speed is unstable. It reduces output ability in high speed range and energy saving in low speed range.
- Less speed it is, lower efficiency it is. Heat is serious in low speed.
- Low adjustment precision, inferior linearity, slow response, not applicable to auto control.
- Motor starts without load, but there is still 5 times of rated current. Big start current affects gird stability.
- Hydraulic coupling has to connect with shaft of motor and machine, not applicable to reform project. When hydraulic coupling is broken, machine can not work because there is no bypass circuit. In this case, machine has to stop to repair.
- Serious oil leakage pollutes environment heavily. Inferior reliability and difficult maintenance waste labor and affect production.
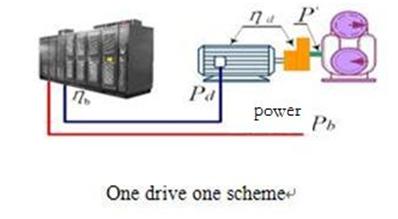
Frequency Inverter energy saving principle
Character curve of dusting fan is following:
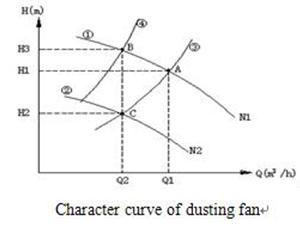
① is curve of running at speed N1, ② is curve of running at N2, ③④ is resistance curve of pipe network. In first load state, load works at A, flow is Q1, pressure is H1. If load still works at constant speed of N1, flow is adjusted to Q2 by damper, pressure will rise to H3, work point moves to B. Resistance curve of pipe network changes to④ from ③.
At A and B, load power: PA=H1×Q1, PB=H3×Q2. Q2<Q1, but H3>H1, actual power reducing is limited.
If adjustment does not adopt damper control, resistance curve ③ does not change. Reduce flow by adjusting load speed, load runs at speed N2, work curve is ②. Load works at C, flow is still Q2, pressure is H2.
Compare B and C, shaft power reducing is: ΔP=PB- PC=(H3–H2)×Q2
In the case of resistance character unchanging, there is relationship between centrifugal fan flow Q, pressure H, shaft power P and speed N:
Q∝N, H∝N2,P∝N3
So,

That is to say, in variable frequency adjustment, in the case of taking no account of efficiency, when flow reduces to half, shaft power of fan lowers 87.5%. This is the reason why frequency inverter has such considerable energy saving effect on fans.
In addition, starting in direct on line brings big impact on power grid and mechanism as well as big noise. Estimation loss of each start-up: Ws=0.5Jwo²(1+r1/r2)Tm/Tm-TL. Square torque character of fan is similar to mechanism character of asynchronous motor in starting, so Tm/Tm-TL=1. But in frequency inverter control, soft start makes start loss small, only 10% of Ws. Therefore, energy saving of start-up is very considerable.
In frequency inverter control, because filter capacitor inside frequency inverter improves power factor, power factor is near to 1 at 50Hz. Work current is far less than rated current. It can save 20% capacity for power grid.
Operation effect
Parameters of 6# dusting fan:
Rated power 710kW, rated voltage 6kV, rated current 89A, power factor 0.816, rated speed 740r/min.
Frequency inverter input values:
High speed (45Hz), current 50~55A; low speed (5Hz), current 1.36A. According to formula: frequency inverter input voltage U1×frequency inverter input current I1×frequency inverter power factor=frequency inverter output voltageU2×industry frequency current I2×motor power factor. Actual operation industry frequency current is: high speed 59~65A, low speed 18A.
In high speed, input current 55A, input voltage 6450V, speed 740r/min;
In low speed, input current 1.3A, input voltage 540V, speed 76r/min.
Make calculation as per frequency inverter display values. Output iron time and non output time rate is 60% and 40%. Yearly work time is 8000h.
In direct on line state, power consumption is
√3 ×Ue×I×cosΦ=1.732×6.450×65×0.816=592.5kW·h
Power cost: 0.5yuan/kW.h, 592.5×8000×0.5=2370124 yuan
In variable frequency state, speed is in direct rate to frequency, relationship of power and speed is:
P/Pe= (n/ne)3
In high speed: P=Pe× (n/ne)3/0.96=739.5kW·h
Power cost: 739.5× (8000×60%)×0.5=1774800 yuan
In low speed: P=Pe× (n/ne)3/0.96=0.74 kW·h
Power cost: 0.74× (8000×40%)×0.5=1184 yuan
Yearly cost saved: 2370124-1774800-1184=594140 yuan (USD 87373). Energy saving rate is 25%. Cost can be repaid in one and half year.
Other benefits of using frequency inverter:
a. Less maintenance
Generally, main purpose of frequency inverter application is to reduce motor speed. Slow start-up and low speed prolong equipment lifetime and reduce impact on pipe. Maintenance period of pipe is reduced and maintenance cost is saved.
b. Less work labour
Variable frequency system adopts computer interlock control between running equipment and standby equipment. System implements automatic operation and related protection and alarm. Work is changed to monitor work from manual work, which makes unmanned operation a reality. It lowers work labor greatly and heightens efficiency, ensures perfect operation.
c. Less impact on grid
With frequency inverter, system implements soft start. Start current is far less than rated current. Start-up time is prolonged, no big impact on power grid. It reduces mechanical damage on motor and prolongs equipment lifetime effectively.
Conclusion
Frequency inverter connects between power source and motor. It is replacing other speed adjustment drives and entering into kinds of industries rapidly as its safety and reliability. Its main purpose is to reduce equipment speed. It heightens automatization level, meets requirement of production technologies as well as energy saving. Furthermore, frequency inverter reduces maintenance cost greatly and brings considerable economic benefits for company. Frequency inverter plays an important role in energy saving of motor system.
Post a Comment:
You may also like: