Category
- Products
- FAQ
- Contact us
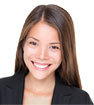
Frequency inverter manufacturers
How to build a reliable frequency converter system?
Frequency converters general applications:
When it comes to putting together a motor control system it takes a lot more information then just the motor size. Many other factors come into play. For example:
If you have equipment needing precise and constant adjustments in motor speed, a converter may be what you need. With the use of a frequency converter, smooth startups and adjustable speeds can be obtained. Our frequency converter systems provide the latest in microprocessor technology to control and monitor what your motors are doing.
The following is a description of both the required and optional components needed to quote and build a frequency converter system. We will design and build a motor control system as required by the customer.
Motor Information
If available, the best information would be to have the motor nameplate data. This is not absolutely necessary, but will help to insure that the integration of the frequency converter and motor is the best possible. As a minimum, the following is required: voltage, horsepower and FLA.
The size of a frequency converter is usually specified by its horsepower. A better way would be to specify the maximum expected current requirement. If the load will demand current at greater than 200% of its rated current, then the frequency converter will trip to protect itself. If this current demand is for short duration then no damage will occur to the motor and the tripping will be considered a "nuisance trip". To avoid this situation the frequency converter should be sized for the maximum expected current.
Load Information
What type of machine is being started? If the machine has a large rotating mass such as a band saw it will be difficult to both start and stop. If the machine has all of its mass concentrated about the rotating axis then it will be much easier to start and stop. This sort of information is critical to insure a successful motor control system.
Environmental Conditions
Where will the starter enclosure be located? Will it be exposed to sunshine, water, sawdust, etc.? Knowing this information will allow us to select the proper type of electrical enclosure.
Isolation Contactor
An isolation contactor is not a required item, but is a good idea to include when dynamic braking is being used. Without the isolation contactor the frequency converter will receive power all the time. The isolation contactor is used to remove the power from the frequency converter on evenings, weekends, or during any shutdown period. If braking with a brake resistor is used, it is possible to turn on the braking circuit unintentionally when the mill is not running. This is caused by the voltage level on the input to the frequency converter rising to a level greater than the normal voltage while there is no demand at the mill. This will cause the voltage output of the frequency converter to also rise. Since the braking circuit is triggered by voltage level, the brake resistor may become energized. During normal operation the resistor will see current for very brief periods of time. If the resistor sees current continuously for an entire weekend it will become quite hot and could possibly start a fire.
Line Reactor
The line reactor is used to absorb any expected voltage spikes. This will protect the input stage of the frequency converter. This is not always required, but is pretty cheap protection.
Load Reactor
The load reactor is also used to absorb voltage spikes. These spikes are created by the frequency converter and may damage the insulation of the motor windings. The load reactor is used when the length of the cable run from the frequency converter to the motor is very long, or when multiple motors are run from one frequency converter.
External Overload Protection
Motor overload protection is provided in the frequency converter’s circuitry. However, if multiple motors are run from a single frequency converter then individual overload protection will need to be added.
Brake Chopper
The brake chopper is external circuitry that must be added to use dynamic braking with some sizes of frequency converters. The brake chopper will divert current to the external brake resistor when the output voltage rises. Most small frequency converters, less than 25 Hp, have internal brake choppers. With these smaller frequency converters a brake resistor can be connected directly to the brake terminals on the frequency converter. The brake chopper is not included on the larger frequency converters due to the heat that would be created within the frequency converter during braking. With the smaller frequency converters the current levels are lower and the heat is not a problem.
Circuit Disconnect
A circuit disconnect is required in front of the frequency converter. This can be either a circuit breaker, a non-fused disconnect switch, or a fused disconnect switch. The disconnect switch can either be provided by the customer in a separate enclosure feeding into our enclosure, or we can install the disconnect with the frequency converter.
The Canadian Electrical Code requires that each branch motor circuit be fused and that the disconnect switch be in sight of the motor starter cabinet. Some combination of disconnecting and fusing must be included by the customer and SDL.
Operator Controls
What type of control circuit will the customer be looking for? Do they simply want to use start and stop buttons, or will there be more to the control strategy? We need this information so that we can bring all the control functions to terminal strips for easy connection by the customer’s electrician. This information is not completely necessary for the preparation of a quote, but will make the quote more accurate.
Control Logic
The control circuit varies in complexity depending on the options. It consists of push buttons, indicator lights, relays, timers, option cards and possibly a programmable logic controller and program.
The cost of a PLC and programming time can be quite expensive, but is cost effective for a sophisticated control strategy. Costing of the PLC and program will be estimated on an individual basis.
- Lumber processing (chipping heads, hoists, conveyors)
- Mining
- Gravel & Aggregate
- Plastics
- Pump applications for agriculture & sewage projects
- Fan and compressor applications for food processing and refrigeration
- Soft Starting/or Rapid Starts
- Soft Stopping & Aggressive Stops
- Reversing at different accel rates than forward
- Dynamic Braking
When it comes to putting together a motor control system it takes a lot more information then just the motor size. Many other factors come into play. For example:
- what kind of equipment is this motor running
- what kind of torque is required
- how often is the motor started
- what are the control requirements
- what type of operator interface is desired, etc.
If you have equipment needing precise and constant adjustments in motor speed, a converter may be what you need. With the use of a frequency converter, smooth startups and adjustable speeds can be obtained. Our frequency converter systems provide the latest in microprocessor technology to control and monitor what your motors are doing.
The following is a description of both the required and optional components needed to quote and build a frequency converter system. We will design and build a motor control system as required by the customer.
Motor Information
If available, the best information would be to have the motor nameplate data. This is not absolutely necessary, but will help to insure that the integration of the frequency converter and motor is the best possible. As a minimum, the following is required: voltage, horsepower and FLA.
The size of a frequency converter is usually specified by its horsepower. A better way would be to specify the maximum expected current requirement. If the load will demand current at greater than 200% of its rated current, then the frequency converter will trip to protect itself. If this current demand is for short duration then no damage will occur to the motor and the tripping will be considered a "nuisance trip". To avoid this situation the frequency converter should be sized for the maximum expected current.
Load Information
What type of machine is being started? If the machine has a large rotating mass such as a band saw it will be difficult to both start and stop. If the machine has all of its mass concentrated about the rotating axis then it will be much easier to start and stop. This sort of information is critical to insure a successful motor control system.
Environmental Conditions
Where will the starter enclosure be located? Will it be exposed to sunshine, water, sawdust, etc.? Knowing this information will allow us to select the proper type of electrical enclosure.
Isolation Contactor
An isolation contactor is not a required item, but is a good idea to include when dynamic braking is being used. Without the isolation contactor the frequency converter will receive power all the time. The isolation contactor is used to remove the power from the frequency converter on evenings, weekends, or during any shutdown period. If braking with a brake resistor is used, it is possible to turn on the braking circuit unintentionally when the mill is not running. This is caused by the voltage level on the input to the frequency converter rising to a level greater than the normal voltage while there is no demand at the mill. This will cause the voltage output of the frequency converter to also rise. Since the braking circuit is triggered by voltage level, the brake resistor may become energized. During normal operation the resistor will see current for very brief periods of time. If the resistor sees current continuously for an entire weekend it will become quite hot and could possibly start a fire.
Line Reactor
The line reactor is used to absorb any expected voltage spikes. This will protect the input stage of the frequency converter. This is not always required, but is pretty cheap protection.
Load Reactor
The load reactor is also used to absorb voltage spikes. These spikes are created by the frequency converter and may damage the insulation of the motor windings. The load reactor is used when the length of the cable run from the frequency converter to the motor is very long, or when multiple motors are run from one frequency converter.
External Overload Protection
Motor overload protection is provided in the frequency converter’s circuitry. However, if multiple motors are run from a single frequency converter then individual overload protection will need to be added.
Brake Chopper
The brake chopper is external circuitry that must be added to use dynamic braking with some sizes of frequency converters. The brake chopper will divert current to the external brake resistor when the output voltage rises. Most small frequency converters, less than 25 Hp, have internal brake choppers. With these smaller frequency converters a brake resistor can be connected directly to the brake terminals on the frequency converter. The brake chopper is not included on the larger frequency converters due to the heat that would be created within the frequency converter during braking. With the smaller frequency converters the current levels are lower and the heat is not a problem.
Circuit Disconnect
A circuit disconnect is required in front of the frequency converter. This can be either a circuit breaker, a non-fused disconnect switch, or a fused disconnect switch. The disconnect switch can either be provided by the customer in a separate enclosure feeding into our enclosure, or we can install the disconnect with the frequency converter.
The Canadian Electrical Code requires that each branch motor circuit be fused and that the disconnect switch be in sight of the motor starter cabinet. Some combination of disconnecting and fusing must be included by the customer and SDL.
Operator Controls
What type of control circuit will the customer be looking for? Do they simply want to use start and stop buttons, or will there be more to the control strategy? We need this information so that we can bring all the control functions to terminal strips for easy connection by the customer’s electrician. This information is not completely necessary for the preparation of a quote, but will make the quote more accurate.
Control Logic
The control circuit varies in complexity depending on the options. It consists of push buttons, indicator lights, relays, timers, option cards and possibly a programmable logic controller and program.
The cost of a PLC and programming time can be quite expensive, but is cost effective for a sophisticated control strategy. Costing of the PLC and program will be estimated on an individual basis.
Post a Comment:
You may also like: