Category
- Products
- FAQ
- Contact us
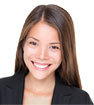
Frequency inverter manufacturers
Understanding Frequency inverter
Nowadays, frequency inverters are widely used in many power systems, such as mechanical drive systems and control systems. It is important to improve the frequency inverter control strategy to make it adaptable to different situations. The frequency conversion method can be divided to two types: the voltage controlled frequency conversion and the current controlled frequency conversion.
Voltage frequency transformation (V/F) is one of the widely used voltage controlled frequency conversion methods. There are two most commonly used modulation modes for V/F: the sinusoidal pulse width modulation (SPWM) and the space vector pulse width modulation (SVPWM). SPWM can basically meet the requirements in transmission, and it is also the most widely used method in frequency inverter, but when the motor runs at a low frequency, the maximum output torque decreases. The purpose of SVPWM is to generate motor circular magnetic field trajectory, which can improve the voltage utilization, but SVPWM can not adjust the torque conveniently.
Conventional voltage controlled frequency inverter has bad performance on dynamic response and steady state accuracy of the frequency converter output current. What's more, the waveform distortion of the output sinusoidal current is serious, which contains a lot of high-frequency harmonics, resulting in a decline of efficiency for the motor.
Vector control is a high-performance current controlled frequency conversion method. The vector control method uses Park transformation, Clarke transformation, inverse Park transformation and inverse Clarke transformation to decompose the stator current and get covariant with torque and magnetic field. However, this method depends a lot on the parameters of the motor, moreover, the rotor flux can not be measured accurately. For these reasons, the actual performance of the vector control based method is not good. As mentioned before, voltage controlled frequency inverters may not provide sufficient torque for the motor, the current controlled frequency inverter is studied in this paper. A current tracking based control method for frequency inverter is proposed. This method controls the output current of the frequency inverter directly, so the frequency inverter can control the motor output torque more easily, it can also be effective in preventing the occurrence of frequency inverter's overcurrent, and reducing the current fluctuations during the acceleration and deceleration process.
The basic idea of the frequency inverter current tracking method is to track the given sine wave signal based on the motor load, and then change the amplitude or frequency of the given sine wave. For implementation, a three-phase stator current is firstly gotten and compared with the given current signal. The bias current is then calculated, which is then put through a Proportion-Integration regulator. The PWM duty cycle of the inverter part is then regulated to make the three phase stator current approach the given current signal gradually. The current tracking control of the frequency inverter actually constitutes a current closed-loop control system.
Voltage frequency transformation (V/F) is one of the widely used voltage controlled frequency conversion methods. There are two most commonly used modulation modes for V/F: the sinusoidal pulse width modulation (SPWM) and the space vector pulse width modulation (SVPWM). SPWM can basically meet the requirements in transmission, and it is also the most widely used method in frequency inverter, but when the motor runs at a low frequency, the maximum output torque decreases. The purpose of SVPWM is to generate motor circular magnetic field trajectory, which can improve the voltage utilization, but SVPWM can not adjust the torque conveniently.
Conventional voltage controlled frequency inverter has bad performance on dynamic response and steady state accuracy of the frequency converter output current. What's more, the waveform distortion of the output sinusoidal current is serious, which contains a lot of high-frequency harmonics, resulting in a decline of efficiency for the motor.
Vector control is a high-performance current controlled frequency conversion method. The vector control method uses Park transformation, Clarke transformation, inverse Park transformation and inverse Clarke transformation to decompose the stator current and get covariant with torque and magnetic field. However, this method depends a lot on the parameters of the motor, moreover, the rotor flux can not be measured accurately. For these reasons, the actual performance of the vector control based method is not good. As mentioned before, voltage controlled frequency inverters may not provide sufficient torque for the motor, the current controlled frequency inverter is studied in this paper. A current tracking based control method for frequency inverter is proposed. This method controls the output current of the frequency inverter directly, so the frequency inverter can control the motor output torque more easily, it can also be effective in preventing the occurrence of frequency inverter's overcurrent, and reducing the current fluctuations during the acceleration and deceleration process.
The basic idea of the frequency inverter current tracking method is to track the given sine wave signal based on the motor load, and then change the amplitude or frequency of the given sine wave. For implementation, a three-phase stator current is firstly gotten and compared with the given current signal. The bias current is then calculated, which is then put through a Proportion-Integration regulator. The PWM duty cycle of the inverter part is then regulated to make the three phase stator current approach the given current signal gradually. The current tracking control of the frequency inverter actually constitutes a current closed-loop control system.
Post a Comment:
You may also like: