Category
- Products
- FAQ
- Contact us
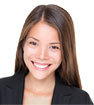
Frequency inverter manufacturers
Why frequency converter has benefits to higher productivity?
Design features benefit to higher productivity include motor type, housing, and materials selected. Built-in components that facilitate high-speed operation also help. An integral braking function is one example, providing safe, fast stops from maximum speed to standstill under maximum load.
Frequency converters that are easy to upgrade also improve productivity. A networked PLC, for example, can remotely update inverter firmware and application data through a single machine interface. If a frequency inverter must be exchanged in the field, its operating system automatically updates from the PLC.
Downtime is generally the converse of productivity. In applications utilizing frequency converter, downtime is primarily caused by trips or faults, and failures. Minimizing these is key to maximizing the frequency converter's benefits to higher productivity. Thanks to powerful microprocessor technology and advanced algorithms, sophisticated trip-avoidance functions are now also being incorporated in inverters. Such functions adjust output frequency and voltage to keep the frequency converter running through system disturbances that might otherwise have caused the frequency converter to trip out. Every trip avoided means uninterrupted production.
Frequency converters must be able to communicate with other devices and in many cases control entire processes. By precisely controlling process speed, for example, a frequency inverter can continuously modify throughput to meet demand changes. To coordinate more than one aspect of a process, frequency converters must be able to communicate with many devices. To illustrate, on a bottle labeling system, the frequency inverter must be able to precisely coordinate the upper level controller, bottle feed, and labeler to produce a quality product.
Energy savings is key benefit to productivity. On variable torque applications, such as a fan for airflow control, normally the motor connected to the fan operates across the line. This means the motor always operates at a fixed speed: 1,800 rpm for a four-pole motor, for example. The result is consistent energy demand from the power system. However, if the system requires varied airflow, then using a frequency converter can save a lot of energy. The power requirement varies as the cube of the speed, so if airflow requirements are only half the air volume, then the frequency converter can operate at half the output frequency - resulting in motor speed at a low 900 rpm. The resultant power requirement is only 1/8th of that required to operate at full speed.
Ease of communication is a must. frequency converter packages must be able to talk to everything from PLCs to the simplest switches. Speed optimization features also improve productivity, as do remote operator interfaces that link and coordinate multiple frequency inverters.
Frequency converters that are easy to upgrade also improve productivity. A networked PLC, for example, can remotely update inverter firmware and application data through a single machine interface. If a frequency inverter must be exchanged in the field, its operating system automatically updates from the PLC.
Downtime is generally the converse of productivity. In applications utilizing frequency converter, downtime is primarily caused by trips or faults, and failures. Minimizing these is key to maximizing the frequency converter's benefits to higher productivity. Thanks to powerful microprocessor technology and advanced algorithms, sophisticated trip-avoidance functions are now also being incorporated in inverters. Such functions adjust output frequency and voltage to keep the frequency converter running through system disturbances that might otherwise have caused the frequency converter to trip out. Every trip avoided means uninterrupted production.
Frequency converters must be able to communicate with other devices and in many cases control entire processes. By precisely controlling process speed, for example, a frequency inverter can continuously modify throughput to meet demand changes. To coordinate more than one aspect of a process, frequency converters must be able to communicate with many devices. To illustrate, on a bottle labeling system, the frequency inverter must be able to precisely coordinate the upper level controller, bottle feed, and labeler to produce a quality product.
Energy savings is key benefit to productivity. On variable torque applications, such as a fan for airflow control, normally the motor connected to the fan operates across the line. This means the motor always operates at a fixed speed: 1,800 rpm for a four-pole motor, for example. The result is consistent energy demand from the power system. However, if the system requires varied airflow, then using a frequency converter can save a lot of energy. The power requirement varies as the cube of the speed, so if airflow requirements are only half the air volume, then the frequency converter can operate at half the output frequency - resulting in motor speed at a low 900 rpm. The resultant power requirement is only 1/8th of that required to operate at full speed.
Ease of communication is a must. frequency converter packages must be able to talk to everything from PLCs to the simplest switches. Speed optimization features also improve productivity, as do remote operator interfaces that link and coordinate multiple frequency inverters.
Post a Comment:
You may also like: