Category
- Products
- FAQ
- Contact us
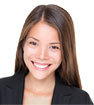
Frequency inverter manufacturers
Because it is difficult to change the frequency of an AC sine wave while in the AC mode, the first job of a frequency converter is to convert the wave to DC. As you will see a little later, it is relatively easy to manipulate DC in order to make it look like AC. The first component of all frequency converters is a device known as a rectifier or converter and it is shown to the left of the figure below.
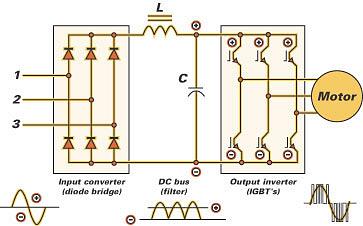
The rectifier circuit converts AC to DC and does so in much the same manner as those of a battery charger or arc welder. It uses a diode bridge to limit the travel of the AC sine wave to one direction only. The result is a fully rectified AC wave form that is interpreted by a DC circuit as a native DC wave form. Three phase frequency converters accept three separate AC input phases and convert them to a single DC output. Most three phase frequency converters can also accept single phase (230V or 460V) power but, since there are only two incoming legs, the frequency converters output (HP) must be derated because the DC current produced is reduced proportionally. On the other hand, true single phase frequency converters (those that control single phase motors) utilize a single phase input and produce a DC output that is proportional to the input.
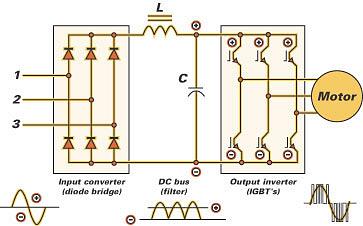
The rectifier circuit converts AC to DC and does so in much the same manner as those of a battery charger or arc welder. It uses a diode bridge to limit the travel of the AC sine wave to one direction only. The result is a fully rectified AC wave form that is interpreted by a DC circuit as a native DC wave form. Three phase frequency converters accept three separate AC input phases and convert them to a single DC output. Most three phase frequency converters can also accept single phase (230V or 460V) power but, since there are only two incoming legs, the frequency converters output (HP) must be derated because the DC current produced is reduced proportionally. On the other hand, true single phase frequency converters (those that control single phase motors) utilize a single phase input and produce a DC output that is proportional to the input.
The current tracking frequency inverter system contains five parts: the current waveform generation part, the PI regulator, the PWM part, the inverter and the motor, the first three belong to control part, and last two belong to power part, all of these form a current closed loop feedback system. The framework of the system is shown in Figure 1. In the diagram, PWM1 to PWM6 represents 6 PWM signals input to inverter part, U, V and W represent 3 output voltages of the three-phase bridge, M represents an induction machine. In the current waveform generation module, 3 sine waves are generated as the standard three phases by a 32-bit microcontroller, the phase difference between each two phases is 120o. iw and iv are the two output currents of the frequency inverter, which are measured by hall current sensors. The three currents satisfy that iu + iv + iw = 0, so the third phase current can be obtained by the formula: iu = -iv -iw. The proportional-integral regulator (PI regulator) uses the two feedback currents and the three standard sine signals to calculate a new duty cycle for each bridge.
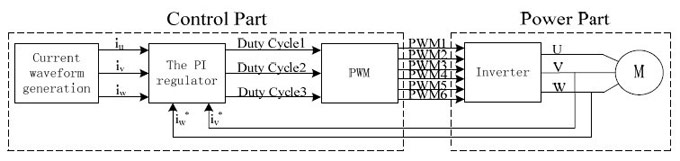
Nowadays, frequency inverters are widely used in many power systems, such as mechanical drive systems and control systems. It is important to improve the frequency inverter control strategy to make it adaptable to different situations. The frequency conversion method can be divided to two types: the voltage controlled frequency conversion and the current controlled frequency conversion.